回转窑处理钢铁企业含锌粉尘技术探讨
2015-04-30
樊波,王艳民,全强,郭豪
中冶京诚工程技术有限公司
1 前言
钢铁厂含铁尘泥是在钢铁生产过程中从不同生产工艺流程的除尘系统中排出的粉尘和污泥的统称。钢铁厂产生的含铁尘泥,如烧结机头除尘灰、高炉煤气除尘灰、炼钢除尘灰、连铸污泥、热轧污泥以及各种环境集尘等,其主要成分是铁,并含有部分碳、锌、铅、钾、钠等。
此前,这些含铁粉尘大部分以返回烧结等方式进行处理利用,但这会造成锌、铅、钾、钠等有害元素在高炉流程中的不断富集,锌的富集对高炉冶炼及长寿带来不利影响;高炉炼铁过程中,炉料中的锌除一部分随煤气、炉渣排出外,高炉内存在锌的循环富集,而锌的氧化反应能引起耐材膨胀,破坏砖衬,且易产生结瘤。碱金属(K、Na)在高炉内易形成低熔点物质,与耐材的基质发生化学反应,引起耐材强度下降和异常膨胀。
随着企业认识的提高及技术的进步,以及环保要求,钢铁企业含铁尘泥进行资源化回收利用逐渐得到重视,其不仅可以减少废弃物排放量,有效利用资源,节省能源,对钢铁企业发展循环经济、实现清洁生产具有积极意义。
钢铁厂含铁尘泥的利用需要解决锌及碱金属富集问题,因此,钢铁厂含铁尘泥的综合回收利用应综合考虑不同的利用原则。含锌、碱金属较低的含铁尘泥可以返回烧结工序利用。对于含锌、碱金属较高的含铁尘泥,应采用能够有效分离铁和锌及碱金属的综合利用工艺。
2 含锌粉尘处理方式简析
含锌尘泥的处理方式主要有湿法工艺、火法工艺及湿法及火法联合工艺等。湿法工艺流程相对复杂,生产效率较低,且要求原料含锌较高。而火法工艺处理含锌尘泥效率高、处理能力大、对原料适应性强,目前得到工业生产应用及正在研发的火法处理工艺有多种,如转底炉工艺、回转窑工艺、等离子炉工艺、韦氏炉工艺、竖式炉工艺、垂直喷射火焰炉工艺、电炉还原工艺等。其中回转窑及转底炉是目前世界上处理钢厂含锌粉尘技术相对成熟,应用较多的工艺技术,也是目前国内比较受关注的用于处理钢厂含锌铅粉尘的技术。
转底炉处理含锌粉尘工艺,其生产规模大、产品质量较稳定、产品附加值高、反应速度快、脱除锌铅率高,并可脱除部分碱金属,但投资相对较高。回转窑法工艺设备简单、技术成熟、投资较低,能耗较高,窑内易结圈,但回转窑生产规模灵活,尤其适用于粉尘量较少的企业,使得回转窑处理含锌粉尘工艺具有一定优势。
3 回转窑处理含锌粉尘技术
3.1概述
回转窑处理含锌物料于1929年起就应用于德国某企业,此后不断发展,在德国、法国、西班牙、意大利、美国、日本等国均有采用回转窑处理含锌物料的工业生产线,是历史悠久且目前应用最为广泛的含锌烟尘处理工艺。
初步统计,国内钢铁企业或独立企业已建及在建的回转窑处理含锌粉尘生产线有近20条,是目前国内处理含锌粉尘最主要的的火法处理方式之一,而且由于其诸多相对优势,正在不断发展。
回转窑法是从钢铁厂废料中分离锌并回收含铁料而发展起来的,回转窑处理含锌的物料时,物料与还原剂(焦粉或煤粉)混合均匀,从窑尾加入具有一定倾斜度的回转窑内,随着窑的转动,炉料翻滚,并从一端向另一端流动。窑头燃烧室产生的高温炉气与物料逆向流动,炉料中的金属氧化物与还原剂良好接触而被还原。窑内沿窑长各带的温度不同,最高温度可达1100~1300℃。锌在窑温下蒸发并与排出的烟气一起离开回转窑,经过收集装置富集锌。处理高炉瓦斯灰等含锌粉尘时,约90%的锌进入气相。窑渣采用水进行快速冷却,进一步分选处理。其典型工艺流程图见图1。
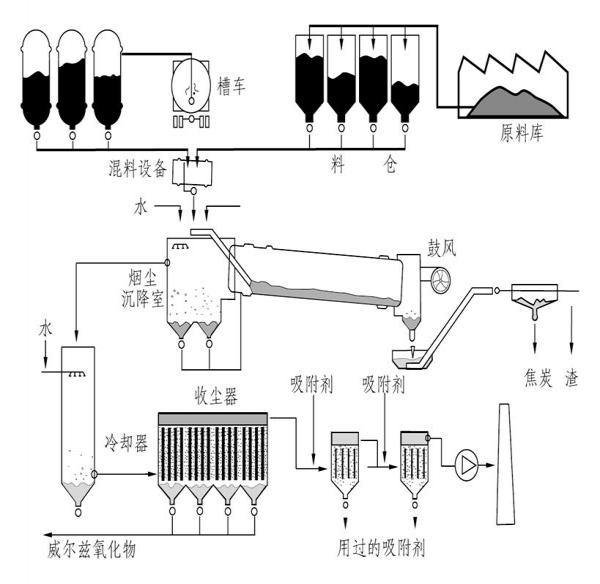
3.2回转窑处理含锌粉尘工艺分析
典型的回转窑综合处理含锌粉尘工艺可以分为三个系统:回转窑直接还原系统、锌焙砂处理系统、窑渣选铁系统。
3.2.1回转窑直接还原系统
回转窑直接还原系统工艺流程:将高炉炼铁烟尘与焦粉按照一定的比例配料后通过胶带输送机送入回转窑中,挥发窑反应区温度为1000~1300℃,窑尾烟气温度约为400~500℃,炼铁烟尘中的有价金属锌、铟、铅、铋、锡、镉等在回转窑内被还原,挥发进入气相中被氧化成氧化物,经降温后被收集在烟道及布袋收尘器内,随后送入锌焙砂窑系统或外卖,烟气再由风机送至脱硫塔洗涤脱硫后,由烟囱排放;回转窑内的窑渣在水淬熄火降温后送入选铁处理工序。典型工艺流程见图2。
……
相关文章
[错误报告] [推荐] [收藏] [打印] [关闭] [返回顶部]