抓住时机发展我国的直接还原铁
2010-06-23
韦俊贤
Ⅰ-1现状
进入21世纪以来,我国钢铁工业快速发展,粗钢产量年均增长21.1%。2008年,粗钢产量达到5亿吨,占全球产量的38%,国内粗钢表观消费量4.53亿吨,直接出口折合粗钢6000万吨,占世界钢铁贸易量的15%。2007年,规模以上钢铁企业完成工业增加值9936亿元,占全国GDP的4%,实现利润2436亿元,占工业企业利润总额的9%,直接从事钢铁生产的就业人数358万。2009年我国钢、铁、焦的产量分别达到56784万吨、54375万吨、34502万吨,创历史新高,见图1。
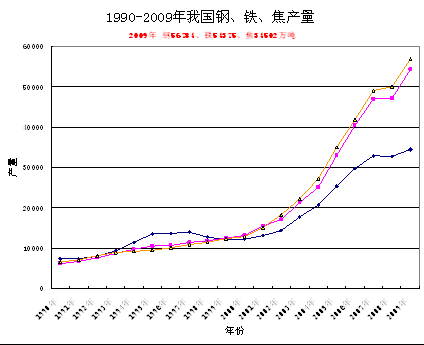
钢铁产品基本满足国内需要,部分关键品种达到国际先进水平,但相当数量的优质钢材还需进口。
钢铁产业有力支撑和带动了相关产业的发展,促进了社会就业,对保障国民经济又好又快发展做出了重要贡献。
Ⅰ-2特点
我国钢铁工业的特点:以长流程为主,铁钢比高,焦炭消耗多,电炉钢比低,污染严重。
图2 我国和世界的铁钢比

图3 我国和世界电炉钢比

Ⅰ-3 问题
钢铁业的发展虽然喜人,但是,钢铁产业长期粗放发展积累的矛盾日益突出,也令人担忧。
一是盲目投资严重,产能总量过剩。截至2008年底,我国粗钢产能达到6.6亿吨,超出实际需求约1亿吨。加上正在兴建和拟建的曹妃甸、鲅鱼圈、湛江、防城港等千万吨级的大型钢铁企业,我国钢的产能实际已经超过7亿吨。我国机焦的产能达到4.15亿吨、再加上无回收炉2500万吨、半焦炉2500万吨,焦炭产能共计4.6亿吨。
二是创新能力不强,先进生产技术、高端产品研发和应用还主要依靠引进和模仿,一些高档关键品种钢材仍需大量进口,消费结构处于中低档水平。
三是产业布局不合理,大部分钢铁企业分布在内陆地区的大中型城市,受到环境容量、水资源、运输条件、能源供应等因素的严重制约。
四是产业集中度低,粗钢生产企业平均规模不足100万吨,排名前5位的企业钢产量仅占全国总量的28.5%。
五是资源控制力弱,国内铁矿资源禀赋低,高炉炼铁必须的铁矿石和炼焦煤供不应求。铁矿自给率不足50%,从2008年起我国已成为炼焦煤的净进口国,2009年我国进口了3449万吨炼焦煤。在国内外铁矿石和焦炭价格飞涨的情况下,企业生产成本升高,生产运营艰难。
钢铁业的发展虽然喜人,但是,钢铁产业长期粗放发展积累的矛盾日益突出,也令人担忧。
一是盲目投资严重,产能总量过剩。截至2008年底,我国粗钢产能达到6.6亿吨,超出实际需求约1亿吨。加上正在兴建和拟建的曹妃甸、鲅鱼圈、湛江、防城港等千万吨级的大型钢铁企业,我国钢的产能实际已经超过7亿吨。我国机焦的产能达到4.15亿吨、再加上无回收炉2500万吨、半焦炉2500万吨,焦炭产能共计4.6亿吨。
二是创新能力不强,先进生产技术、高端产品研发和应用还主要依靠引进和模仿,一些高档关键品种钢材仍需大量进口,消费结构处于中低档水平。
三是产业布局不合理,大部分钢铁企业分布在内陆地区的大中型城市,受到环境容量、水资源、运输条件、能源供应等因素的严重制约。
四是产业集中度低,粗钢生产企业平均规模不足100万吨,排名前5位的企业钢产量仅占全国总量的28.5%。
五是资源控制力弱,国内铁矿资源禀赋低,高炉炼铁必须的铁矿石和炼焦煤供不应求。铁矿自给率不足50%,从2008年起我国已成为炼焦煤的净进口国,2009年我国进口了3449万吨炼焦煤。在国内外铁矿石和焦炭价格飞涨的情况下,企业生产成本升高,生产运营艰难。
图4 我国进口铁矿依存度


六是流通秩序混乱。钢铁产品经销商过多,投机经营倾向较重。
在这种背景下,国家主管部门制定了《钢铁产业调整与振兴规划》,严格控制新增产能,不再核准和支持单纯新建、扩建产能的钢铁项目,所有项目必须以淘汰落后为前提。2010年底前,淘汰300立方米及以下高炉产能5340万吨,20吨及以下转炉、电炉产能320万吨;2011年底前再淘汰400立方米及以下高炉、30吨及以下转炉和电炉,相应淘汰落后炼铁能力7200万吨、炼钢能力2500万吨。实施淘汰落后、建设钢铁大厂的地区和其它有条件的地区,要将淘汰落后产能标准提高到1000立方米以下高炉及相应的炼钢产能。
在这种背景下,国家主管部门制定了《钢铁产业调整与振兴规划》,严格控制新增产能,不再核准和支持单纯新建、扩建产能的钢铁项目,所有项目必须以淘汰落后为前提。2010年底前,淘汰300立方米及以下高炉产能5340万吨,20吨及以下转炉、电炉产能320万吨;2011年底前再淘汰400立方米及以下高炉、30吨及以下转炉和电炉,相应淘汰落后炼铁能力7200万吨、炼钢能力2500万吨。实施淘汰落后、建设钢铁大厂的地区和其它有条件的地区,要将淘汰落后产能标准提高到1000立方米以下高炉及相应的炼钢产能。
Ⅱ 从长流程向短流程转变是钢铁工业发展的客观规律
世界钢铁工业发展的情况表明,钢铁生产工艺从长流程向短流程的发展是各国钢铁工业发展的必然规律。
Ⅱ-1国外钢铁工业发的实例
以美国和日本为例:
美国钢铁、焦炭工业发展100年多来的情况,大体可分三个阶段:1951年焦炭产量上升最高峰7930万吨时,钢产量为9542万吨,焦钢比为0.83(焦炭产量比钢产量)。之后,焦炭产量开始下降。到1973年钢产量上升到最高峰13678万吨时,焦炭产量下降为6340万吨,焦钢比降为0.47,比1951年减少0.36。再后,钢产量开始下降,见图5 。
世界钢铁工业发展的情况表明,钢铁生产工艺从长流程向短流程的发展是各国钢铁工业发展的必然规律。
Ⅱ-1国外钢铁工业发的实例
以美国和日本为例:
美国钢铁、焦炭工业发展100年多来的情况,大体可分三个阶段:1951年焦炭产量上升最高峰7930万吨时,钢产量为9542万吨,焦钢比为0.83(焦炭产量比钢产量)。之后,焦炭产量开始下降。到1973年钢产量上升到最高峰13678万吨时,焦炭产量下降为6340万吨,焦钢比降为0.47,比1951年减少0.36。再后,钢产量开始下降,见图5 。
图5 美国100年来焦炭及生铁、钢产量变化情况 (单位:万吨)


到1988年,美国钢的积累量近60亿吨时,钢产量下降到9063万吨,走向比较平稳的正常生产量。国民经济各行业的能源、交通、港口、城市基础设施、房地产等建设比较完善,当年焦炭产量下降到2890万吨,焦钢比下降为0.31。
美国的焦炭产量由1951年最高峰7930万吨,到2008年下降到1424万吨,焦炭产量减少82%,主要原因,一是炼铁焦比下降;二是1973年以后钢产量逐步减少;三是铁钢比大幅度降低,到2008年底钢积累量为78亿吨,社会返回大量的废钢用于炼钢生产,(多余废钢还大量出口)废钢代替生铁减少消费大量焦炭。铁钢比为0.36。
美国近百年来,钢铁发展与焦炭产量下降的曲线图走势,大体上成喇叭形,约30度角延伸。
日本是世界产钢第二大国,钢铁、焦炭发展的情况如下:
日本1948年钢产量171万吨,经过25年到1973年钢产量上升到11932万吨,之后,钢产量一直波动在11000万吨左右,焦炭产量逐年减少。1984年钢产量10558万吨,焦炭产量为5145万吨,焦钢比为0.49。到2008年钢产量11874万吨,焦炭产量下降为3856万吨,焦钢比下降为0.32。24年间,钢产量波动不大,焦炭产量减少25%。
日本国土小,经济建设速度快,国内的能源、交通、港口、城市基础设施、房地产等建设比较完善,钢材消费走向正常的消费量。
日本到2008年底,60年来,钢积累量为47亿吨,返回大量的废钢代替生铁炼钢,焦炭产量较大幅度的减少。日本钢铁发展与焦炭产量下降的曲线图,大体上形成喇叭形约15度延伸,见图6。
美国的焦炭产量由1951年最高峰7930万吨,到2008年下降到1424万吨,焦炭产量减少82%,主要原因,一是炼铁焦比下降;二是1973年以后钢产量逐步减少;三是铁钢比大幅度降低,到2008年底钢积累量为78亿吨,社会返回大量的废钢用于炼钢生产,(多余废钢还大量出口)废钢代替生铁减少消费大量焦炭。铁钢比为0.36。
美国近百年来,钢铁发展与焦炭产量下降的曲线图走势,大体上成喇叭形,约30度角延伸。
日本是世界产钢第二大国,钢铁、焦炭发展的情况如下:
日本1948年钢产量171万吨,经过25年到1973年钢产量上升到11932万吨,之后,钢产量一直波动在11000万吨左右,焦炭产量逐年减少。1984年钢产量10558万吨,焦炭产量为5145万吨,焦钢比为0.49。到2008年钢产量11874万吨,焦炭产量下降为3856万吨,焦钢比下降为0.32。24年间,钢产量波动不大,焦炭产量减少25%。
日本国土小,经济建设速度快,国内的能源、交通、港口、城市基础设施、房地产等建设比较完善,钢材消费走向正常的消费量。
日本到2008年底,60年来,钢积累量为47亿吨,返回大量的废钢代替生铁炼钢,焦炭产量较大幅度的减少。日本钢铁发展与焦炭产量下降的曲线图,大体上形成喇叭形约15度延伸,见图6。
图6 日本近50年来钢、生铁、焦炭产量变化情况 (单位:万吨)


中国是发展中国家,建国前是个农业大国,建国初期钢铁工业经过十几年建设有了一些发展,但钢铁生产仍然比较落后,炼钢用生铁都是一吨多,消费焦炭比较高,1977年钢产量2374万吨,焦炭产量3928万吨,焦钢比为1.654。1978年改革开放后,国民经济各行业发展比较快,钢铁工业技术水平不断提高,炼钢耗生铁大幅度下降,1988年焦钢比降低到1.028,2009年降低到0.607。
图7 中国1978-2008年钢、铁、焦炭产量情况及预测 (单位:万吨)


Ⅱ-2钢铁生产从长流程向短流程的转变是客观规律
随着各国钢铁蓄积量的增加和社会废钢量的增长,钢铁工业电炉钢的比例会逐渐增高。目前,中国电炉钢与世界电炉钢比的平均水平大约相差30个百分点。这就是从结构上造成我国钢铁工业能耗高的主要原因。
从世界钢铁工业发展情况看,当一个国家的人均占有钢量超过5吨时,随着社会废钢量的增加,电炉钢的比例就会快速增长,至2007年,主要国家钢铁的蓄积量见图8。
随着各国钢铁蓄积量的增加和社会废钢量的增长,钢铁工业电炉钢的比例会逐渐增高。目前,中国电炉钢与世界电炉钢比的平均水平大约相差30个百分点。这就是从结构上造成我国钢铁工业能耗高的主要原因。
从世界钢铁工业发展情况看,当一个国家的人均占有钢量超过5吨时,随着社会废钢量的增加,电炉钢的比例就会快速增长,至2007年,主要国家钢铁的蓄积量见图8。
图8 1901~2007年主要国家钢铁蓄积量
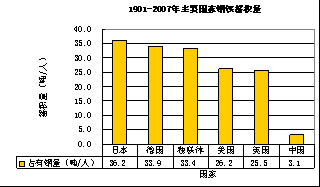
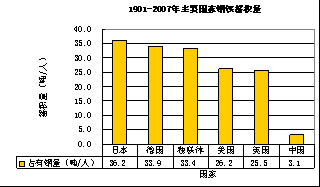
再过十年,中国钢的积累量达到90亿吨左右时,人均占有的钢量将会达到7吨/人,电炉钢将会迅速发展。
目前,中国的电炉钢比虽然只有9%左右,但绝对量并不少,2009年世界钢产量121972万吨,中国钢产量56784万吨,扣除中国其他国家钢产量为65188万吨。按2008年数据推算,2009年世界电炉钢产量约37201万吨,中国电炉钢产量约5920万吨,约占世界电炉钢产量的15.9%。中国电炉钢生产需要大量废钢和直接还原铁。
目前,中国的电炉钢比虽然只有9%左右,但绝对量并不少,2009年世界钢产量121972万吨,中国钢产量56784万吨,扣除中国其他国家钢产量为65188万吨。按2008年数据推算,2009年世界电炉钢产量约37201万吨,中国电炉钢产量约5920万吨,约占世界电炉钢产量的15.9%。中国电炉钢生产需要大量废钢和直接还原铁。
Ⅲ 直接还原铁的发展应与电炉钢发展相适应
Ⅲ-1世界直接还原铁产量
电炉炼钢的主要原料是废钢。而废钢中的错杂元素不断积累会影响钢材的质量。为了稀释废钢中的错杂元素,保证钢材的质量,直接还原铁的产业就由此而生,并持续不断的得到发展。从1970年直接还原铁商业化以来,直接还原铁的产量连年增加,见图9。
Ⅲ-1世界直接还原铁产量
电炉炼钢的主要原料是废钢。而废钢中的错杂元素不断积累会影响钢材的质量。为了稀释废钢中的错杂元素,保证钢材的质量,直接还原铁的产业就由此而生,并持续不断的得到发展。从1970年直接还原铁商业化以来,直接还原铁的产量连年增加,见图9。
图9 1970-2008年世界直接还原铁产量
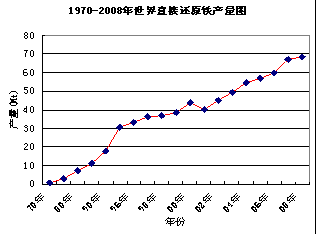
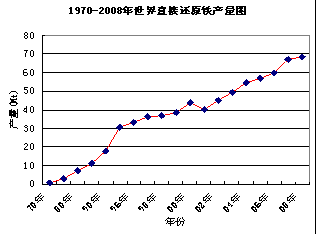
印度缺乏炼焦煤,因而大力发展直接还原铁。印度是世界上直接还原铁产量最多的国家,2009年印度直接还原铁产量2104万吨,钢产量5661万吨,直接还原铁和钢产量的比值为37.6%。我国钢铁工业的快速发展,急速的消耗炼焦煤资源,我国炼焦煤的储量并不多,仅占煤储量的27.6%,见图10。
图10 我国煤储量图
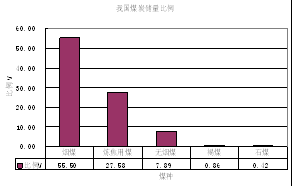
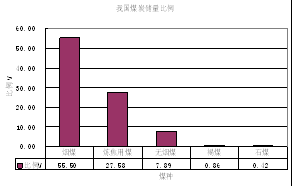
有专家估算,我国炼焦煤在40年左右将消耗殆尽。印度根据自身资源情况发展非高炉炼铁的经验,值得我们借鉴。
Ⅲ-2世界直接还原铁和电炉钢比
直接还原铁主要用做电炉钢的原料,少量用做转炉冷却剂和优质铸件。2009年世界直接还原铁产量和电炉钢量的比值接近20%,中国约为1.2%,见表1。
直接还原铁主要用做电炉钢的原料,少量用做转炉冷却剂和优质铸件。2009年世界直接还原铁产量和电炉钢量的比值接近20%,中国约为1.2%,见表1。
表1 2000~2009年世界和中国直接还原铁产量与电炉钢产量比。
年份 | DRI/电炉钢 % | ||
世界 | 中国 | 其它 | |
2000 | 15.47 | 0.25 | 16.64 |
2001 | 13.69 | 0.46 | 14.86 |
2002 | 14.81 | 0.72 | 16.38 |
2003 | 15.13 | 0.79 | 17.08 |
2004 | 15.68 | 1.03 | 17.68 |
2005 | 16.14 | 0.98 | 18.14 |
2006 | 15.56 | 0.9 | 17.45 |
2007 | 16.44 | 1.2 | 18.56 |
2008 | 16.18 | 1.2 | 16.58 |
2009 | 16.94 | 1.17 | 19.5 |
在2001~2005年之间,全球粗钢产量年增加7%,原材料(废钢、生铁和直接还原铁)的消费量年增长8%,其中直接还原铁的年增长达到10%。
2006~2010年之间,原材料的需求年增长保持5%,直接还原铁和热压块铁的需求量的增幅远远大于其他原材料,目前全球商品热压块铁的产量达到670万吨/年(委内瑞拉430万吨/年、俄罗斯110万吨/年、利比亚70万吨/年、马兰西亚40万吨/年、印度20万吨/年)。需求主要北美(210万吨/年)、远东(120万吨/年)、欧洲(110万吨/年)、中国(100万吨/年)、中东(80万吨/年)、拉美(50万吨/年)。
预计2010年全球商品直接还原铁和热压块铁需求量将增加至960万吨/年。
发达国家的电炉钢冶炼一般直接还原铁的配入量在15~30%,我国直接还原铁的产量很少,进口量也不多,2009年我国进口了177万吨直接还原铁,创历史新高,但摊配在电炉炼钢冶炼中的比例仍然很小。
我国在电炉钢冶炼中大量配入热铁水,这也是我国钢铁工业铁钢比高、能耗高、污染大的原因之一。
在直接还原铁的发展上,我国与世界的差距是很大的。但也表明,直接还原铁在我国有很大的发展空间。
2006~2010年之间,原材料的需求年增长保持5%,直接还原铁和热压块铁的需求量的增幅远远大于其他原材料,目前全球商品热压块铁的产量达到670万吨/年(委内瑞拉430万吨/年、俄罗斯110万吨/年、利比亚70万吨/年、马兰西亚40万吨/年、印度20万吨/年)。需求主要北美(210万吨/年)、远东(120万吨/年)、欧洲(110万吨/年)、中国(100万吨/年)、中东(80万吨/年)、拉美(50万吨/年)。
预计2010年全球商品直接还原铁和热压块铁需求量将增加至960万吨/年。
发达国家的电炉钢冶炼一般直接还原铁的配入量在15~30%,我国直接还原铁的产量很少,进口量也不多,2009年我国进口了177万吨直接还原铁,创历史新高,但摊配在电炉炼钢冶炼中的比例仍然很小。
我国在电炉钢冶炼中大量配入热铁水,这也是我国钢铁工业铁钢比高、能耗高、污染大的原因之一。
在直接还原铁的发展上,我国与世界的差距是很大的。但也表明,直接还原铁在我国有很大的发展空间。
Ⅳ 我国直接还原技术的发展动向
从上世纪50年代开始,我国从未间断过对直接还原技术进行开发研究。目前,我国已建成一批煤基回转窑直接还原铁生产厂,如:天津钢管、富蕴金山矿业、密云、鲁中、喀左等。
还有一些隧道窑直接还原厂分布于新疆、山西、河北、辽宁、吉林、河南、上海、内蒙、云南、山东等十多个省、区。到2009年底,已建成或正在建设的隧道有100多座,设计年产能超过400万吨,由于隧道窑投资低,适合于一些资金缺乏的企业家的需求,因而,建设热潮有增无减。隧道窑生产的直接还原铁质量不稳定,杂质多,不仅造成直接还原铁生产企业经济效益差,更重要的是电炉使用低质量的直接还原铁使炼钢的能耗大幅度上升,隧道窑生产的直接还原铁在电炉炼钢生产中不受欢迎,严重的影响了我国直接还原铁的应用和发展。
上述直接还原铁厂,除天津钢管、富蕴金山矿业的回转窑单机生产能力15万吨/年外,其余生产装置的单机能力均<7.5万吨/年。
自我国直接还原铁实现工业化生产以来,直接还原铁的年产量从未超过60万吨,占世界DRI年产量不足1.0%。
近几年,转底炉在我国得到发展,主要用在复合铁矿的综合利用、钢铁厂粉尘的处理和难选铁矿资源的开发,效果良好。也有的钢铁企业想用转底炉作为预还原装置,为高炉或熔分炉提供直接还原铁,此种工艺过程的技术经济性还有待验证。目前,在建的转底炉近十座,部分已投产运行。
关于转底炉技术,值得关注的是2010年1月,建在美国明尼苏达州的第一个ITMK3商业化工厂已经投产,此法具有产品是“铁粒”、品质好、比重大,抗氧化,易运输,有利于后步熔化工序设备的选择等一系列的优点。我们对此工艺的生产状况应认真进行跟踪观察。
气基竖炉是当今世界直接还原铁生产的主流技术。我国由于天然气资源短缺和价格昂贵,加之供给直接还原铁生产用的高品位球团的生产基地尚未形成,因此,我国至今还没有建成一座气基竖炉生产装置。但是,我国的钢铁和化工工作者,一直在进行对气基竖炉生产工艺的探索和研究。结合中国的国情,正在致力于“煤制气—竖炉”直接还原技术的开发。
从技术上讲,煤制气-竖炉的联合流程在技术上是可行的,印度金达尔厂已经建设了此种工艺流程,煤制气采用的是鲁奇炉高压制气法。
煤制气—竖炉直接还原法在我国倍受关注,一些企业已经做过可行性研究。据不完全统计,约二十多个单位在筹划、规划、设计建设50~160×104t/a的煤制气—竖炉直接还原铁生产线。主要问题是高压煤制气方法的投资太大,经济性欠佳,对于第一个想吃“螃蟹”的企业决心难下。为此,有的单位正在研究低压煤制气和竖炉的联合流程。如果低压煤制气和竖炉的联合流程研发成功,它将彻底改变我国直接还原铁生产的面貌,为我国钢铁工业的发展开辟新的途径。但由于各种原因,至今还没有一个项目进入实质性的运作。
从上世纪50年代开始,我国从未间断过对直接还原技术进行开发研究。目前,我国已建成一批煤基回转窑直接还原铁生产厂,如:天津钢管、富蕴金山矿业、密云、鲁中、喀左等。
还有一些隧道窑直接还原厂分布于新疆、山西、河北、辽宁、吉林、河南、上海、内蒙、云南、山东等十多个省、区。到2009年底,已建成或正在建设的隧道有100多座,设计年产能超过400万吨,由于隧道窑投资低,适合于一些资金缺乏的企业家的需求,因而,建设热潮有增无减。隧道窑生产的直接还原铁质量不稳定,杂质多,不仅造成直接还原铁生产企业经济效益差,更重要的是电炉使用低质量的直接还原铁使炼钢的能耗大幅度上升,隧道窑生产的直接还原铁在电炉炼钢生产中不受欢迎,严重的影响了我国直接还原铁的应用和发展。
上述直接还原铁厂,除天津钢管、富蕴金山矿业的回转窑单机生产能力15万吨/年外,其余生产装置的单机能力均<7.5万吨/年。
自我国直接还原铁实现工业化生产以来,直接还原铁的年产量从未超过60万吨,占世界DRI年产量不足1.0%。
近几年,转底炉在我国得到发展,主要用在复合铁矿的综合利用、钢铁厂粉尘的处理和难选铁矿资源的开发,效果良好。也有的钢铁企业想用转底炉作为预还原装置,为高炉或熔分炉提供直接还原铁,此种工艺过程的技术经济性还有待验证。目前,在建的转底炉近十座,部分已投产运行。
关于转底炉技术,值得关注的是2010年1月,建在美国明尼苏达州的第一个ITMK3商业化工厂已经投产,此法具有产品是“铁粒”、品质好、比重大,抗氧化,易运输,有利于后步熔化工序设备的选择等一系列的优点。我们对此工艺的生产状况应认真进行跟踪观察。
气基竖炉是当今世界直接还原铁生产的主流技术。我国由于天然气资源短缺和价格昂贵,加之供给直接还原铁生产用的高品位球团的生产基地尚未形成,因此,我国至今还没有建成一座气基竖炉生产装置。但是,我国的钢铁和化工工作者,一直在进行对气基竖炉生产工艺的探索和研究。结合中国的国情,正在致力于“煤制气—竖炉”直接还原技术的开发。
从技术上讲,煤制气-竖炉的联合流程在技术上是可行的,印度金达尔厂已经建设了此种工艺流程,煤制气采用的是鲁奇炉高压制气法。
煤制气—竖炉直接还原法在我国倍受关注,一些企业已经做过可行性研究。据不完全统计,约二十多个单位在筹划、规划、设计建设50~160×104t/a的煤制气—竖炉直接还原铁生产线。主要问题是高压煤制气方法的投资太大,经济性欠佳,对于第一个想吃“螃蟹”的企业决心难下。为此,有的单位正在研究低压煤制气和竖炉的联合流程。如果低压煤制气和竖炉的联合流程研发成功,它将彻底改变我国直接还原铁生产的面貌,为我国钢铁工业的发展开辟新的途径。但由于各种原因,至今还没有一个项目进入实质性的运作。
Ⅴ 对我国发展直接还原铁的几点建议
Ⅴ-1 发展直接还原铁有利于节约宝贵的炼焦煤资源,有利于钢铁工业的结构性调整,有利于减少环境污染和减少CO2的排放量,有利于开发复合铁矿、难选铁矿,有利于处理钢铁厂粉尘和有色冶金含铁渣等含铁废弃物,符合循环经济的大政方针,国家对有条件建设直接还原铁的单位应给予政策性的支持。近年来,一些地区和单位已提出气基竖炉建设的规划。由于气基竖炉的建设在我国尚属技术空白,建设者必须具备资源、资金、场地、产品用户等条件才能成功。对于第一个建设者,国家主管部门应当成示范项目给予积极支持。
Ⅴ-2 气基竖炉直接还原铁生产需要高品位铁矿石。根据天津大无缝的经验教训,我国要想发展气基竖炉,必须立足于使用国产铁矿石生产直接还原用的氧化球团。我国一些地区的铁精矿可以选到气基竖炉需要的品位,但对氧化球团的生产工艺还需要做深入的研究工作。
Ⅴ-3 国家主管部门对于“低压粉煤气化-竖炉”的工艺研究应给予鼓励和支持,创新出我国具有自主知识产权的煤制气-气基竖炉新工艺。
Ⅴ-4 我国直接还原技术的研究和发展方兴未艾,我们应该提倡技术协作和技术交流,促进我国直接还原技术的发展。但由于知识产权保护的问题搞得不好,妨碍了直接还原同仁间的交流。我们应当尊重各单位辛勤劳动的成果,尊重各单位的专利技术,如果想利用别人的专利技术,就应按照技术交易的规则来办理。
Ⅴ-5 对直接还原铁厂的建设必须进行认真的可行性研究,不能草率立项,更不能盲目上马,以免造成不必要的损失。
Ⅴ-1 发展直接还原铁有利于节约宝贵的炼焦煤资源,有利于钢铁工业的结构性调整,有利于减少环境污染和减少CO2的排放量,有利于开发复合铁矿、难选铁矿,有利于处理钢铁厂粉尘和有色冶金含铁渣等含铁废弃物,符合循环经济的大政方针,国家对有条件建设直接还原铁的单位应给予政策性的支持。近年来,一些地区和单位已提出气基竖炉建设的规划。由于气基竖炉的建设在我国尚属技术空白,建设者必须具备资源、资金、场地、产品用户等条件才能成功。对于第一个建设者,国家主管部门应当成示范项目给予积极支持。
Ⅴ-2 气基竖炉直接还原铁生产需要高品位铁矿石。根据天津大无缝的经验教训,我国要想发展气基竖炉,必须立足于使用国产铁矿石生产直接还原用的氧化球团。我国一些地区的铁精矿可以选到气基竖炉需要的品位,但对氧化球团的生产工艺还需要做深入的研究工作。
Ⅴ-3 国家主管部门对于“低压粉煤气化-竖炉”的工艺研究应给予鼓励和支持,创新出我国具有自主知识产权的煤制气-气基竖炉新工艺。
Ⅴ-4 我国直接还原技术的研究和发展方兴未艾,我们应该提倡技术协作和技术交流,促进我国直接还原技术的发展。但由于知识产权保护的问题搞得不好,妨碍了直接还原同仁间的交流。我们应当尊重各单位辛勤劳动的成果,尊重各单位的专利技术,如果想利用别人的专利技术,就应按照技术交易的规则来办理。
Ⅴ-5 对直接还原铁厂的建设必须进行认真的可行性研究,不能草率立项,更不能盲目上马,以免造成不必要的损失。
相关文章
[错误报告] [推荐] [收藏] [打印] [关闭] [返回顶部]