废钢铁资源的有效利用是钢铁工业绿色发展的关键
2019-08-14
都兴亚
中国废钢铁应用协会
前言
总结我国钢铁工业发展的历程可以看出,铁矿石一直作为我国钢铁工业生产的主要原料。其原料结构和生产工艺:铁矿石-- 烧结-- 炼铁-- 炼钢-- 轧钢的长流程为主。积极发展电炉炼钢的短流程,即可减少我国钢铁工业对进口铁矿石的过度依赖,又能减少对环境的污染。
废钢铁通常可分为三类:
自产废钢:指钢铁工业生产在冶炼、轧钢等生产工艺过程中,钢铁企业内部产生的废钢铁。
加工废钢:指制造加工业对钢铁产品进行机械加工时产生的废钢铁。
折旧废钢:指各种钢铁制品使用一定年限后报废形成的废钢铁。
加工废钢和折旧废钢统称为社会废钢。
希望通过本次“冶金还原创新发展与资源循环利用”为主题的高峰论坛,更好的推进我国废钢铁(含还原铁)资源合理开发高效利用,提高产业集中度,加强产业上下游之间的深度融合。
1 简述还原铁产业发展的概况
1.1 还原铁产业发展的概况
由碳冶金转为氢冶金是钢铁工业的一场革命,它必将推动钢铁工业转型升级,氢还原炼铁首先要解决氢资源问题。气基竖炉直接还原炼铁普遍采用天然气经转化、重整、裂解生成H2+CO作为还原剂,完成炼铁工艺。
在天然气短缺,长流程为主导的钢铁企业中,采用焦炉煤气为还原剂实现短流程工艺是最佳的选择。其原因有二:
1)长流程中自产焦炉煤气,不需要外购天然气,质量和数量上均满足直接还原工艺的需要;
2)焦炉煤气中含氢60%以上,大大优于天然气,是节能高效的还原剂。
直接还原炼铁技术是成熟的,被钢铁工业普遍认可。气基竖炉单模块产能不断扩大,由年产20万吨逐渐扩大到年产300万吨;
2018年全球直接还原铁产量达9980万吨,比2017年同期增长了12.5%。而我国直接还原铁的产量不到世界总产量的1%,我国还原铁产业发展空间非常巨大,因此,“十三五”及未来一段时间将是我国直接还原铁产业发展的重要时期。
1.2我国直接还原铁产业发展现状
我国的天然气资源短缺,因而直接还原铁开发研究主要集中在煤基直接还原铁工艺(回转窑、隧道窑、转底炉、煤基竖炉等)。回转窑工艺技术在回收铁、鋅和利用红土镍矿生产镍铁、钛精矿生产钛白粉工艺已有成功的案例;转底炉处理含铁尘泥等冶金固废的工艺技术已在国内多家企业运用,如宝钢湛江项目采用转底炉处理含铁尘泥、奠定了转底炉工艺技术在固废利用上的发展定位; 隧道窑多用于生产规模较小的粉末冶金用高品质还原铁块;煤基竖炉万吨中试工厂的稳定运行。
宝钢C-3000大型C OREX熔融还原装置的顺利投产,为我国非高炉炼铁的发展开创了新的局面;山东墨龙HIsmelt熔融还原装置投入生产后,主要指标已明显优于力拓Hismelt的还原工厂指标,所生产的特种铸造生铁磷含量低,基本不含硅、锰等元素,其他5种有害元素(铅、锡、砷、锑、铋)含量非常低,基本满足了我国高端制造业的需求,目前两个项目的生产运行情况良好。
近年来我国对煤制气、竖炉直接还原开展的调研工作,取得了许多可喜的研究成果,为我国发展煤制气、竖炉直接还原技术奠定了良好的基础。
1.3 发展非高炉炼铁的技术优势
欧美国家近年来新上的钢铁项目大多是以非高炉为主的短流程生产线,高功率电炉冶炼时炉料中添加30~50%直接还原铁,可提高生产率10~25%,与传统长流程相比,减排CO2,SO2效果显著,可减少CO2排放40~65%,减少SO2排放约30%。与传统长流程相比,竖炉DRI-电炉冶炼具有流程短,产能高的优点。单套设备产能可达250万吨/年,钢材的物理性能明显提高。
经业内专家多年的研究和实践证明,钢铁企业中实现直接还原-电炉炼钢短流程工艺,具备以下特点和优势。
1)高炉铁吨铁CO2排放量为1600kg,直接还原铁吨铁CO2排放量为800kg。
2)直接还原铁-电炉钢吨钢的生产成本比高炉-转炉炼钢吨钢成本低。
3)根据工厂实际运行统计,焦炉煤气生产直接还原铁是焦炉煤气发电产生经济效益的2.6倍。
4)焦炉煤气中含氢气为60%,而天然气中不氢气,用焦炉煤气生产直接还原铁可以大大降低能耗,并降低纯氧消耗。
5)在钢铁联合企业中,用“五联供”的办法(焦炉煤气、高炉煤气、转炉气、煤制气、天然气)可以做到焦炉煤气供应量的平衡,用顶替出的大量焦炉煤气生产直接还原铁,可谓是一次能源的革命。
6)直接还原铁是纯净铁,最适合于在电炉中生产纯净钢,明显增加钢材的附加值。
7)用100%的球团矿作为直接还原的原料,用100%的直接还原铁作为电炉炼钢的原料,这是当今世界钢铁工业发展的新趋势。
单模块的直接还原装置生产能力已达250万吨/年左右,由此不难看出,直接还原-电炉炼钢短流程具有极大的发展潜力。
8)直接还原与大型铸钢的对接或直接还原-电炉炼钢短流程工艺的复制,项目的落地,成为直接还原电炉炼钢短流程的工业实验厂,将为大型钢铁联合企业的转型升级取得技术和生产经验的有力支持。
长流程与短流程的融合,将构成中国特色钢铁工业发展的方式。大力推进直接还原铁的全面发展,实现我国钢铁工业的绿色发展和转型升级。
2 2018年及今年1-5月份全国废钢铁资源利用情况
2.1 废钢铁消耗总量和废钢综合单耗均创历史新高
2018年,我国生铁、粗钢、钢材(含重复材)产量分别为7.71亿吨、9.28亿吨和11.06亿吨,同比分别增长3%、6.6%和8.5%,粗钢产量再创历史新高。国内表观消费量8.7亿吨,同比增长14.8%,达到历史最高水平,其中国产自给率超过98%。钢铁行业主营业务收入7.65万亿元,同比增长13.8%;实现利润4704亿元,同比增长39.3%。
全国废钢铁消耗总量1.88亿吨,同比增加0.39亿吨,增幅26.9%;废钢单耗202.3kg/t,同比增加24.5kg/t,增幅13.8%。废钢比20.2%,同比增加2.45个百分点。电炉钢比9.8%,同比提高0.5个百分点。
从以上数据表明,我国废钢铁资源利用水平实现了新的突破,到2018年9月已经提前两年三个月完成了“废钢铁产业十三五规划”提出的废钢比达到20%的预期目标,废钢铁产业发展已进入重要转折期,钢铁工业大批量应用废钢铁已进入新的时代。
图表1 2018年全国废钢铁消耗情况
2019年1-5月,我国生铁产量33535万吨,同比增长8.9%;粗钢产量40488万吨,同比增长10.2%。全国废钢铁消耗总量8093万吨,同比增加956万吨,增幅13.4%;废钢单耗199.8KG/T,同比增加6.8KG/T,增幅3.5%,其中转炉废钢单耗156.2KG/T,同比提高16KG/T,增幅11.4%;电炉废钢单耗602.1KG/T,同比下降66.5KG/T,降幅9.9%;废钢比19.9%,同比增加0.6个百分点。电炉钢比9.7%,同比下降0.3个百分点。
2018年,Mysteel调研全国244座电弧炉,产能为1.31亿吨。(按照工信部最新电炉产能核定)从省份来看,江苏、广东、山东、四川、湖北等地电弧炉产能较多。电弧炉主要分布在废钢资源丰富或电力资源丰富的区域。数据同时显示,全国53家独立电弧炉钢厂产能4396万,实际产量2971.85万,全年产能利用率67.6%。
2019年上半年,电弧炉开工率、产能利用率持续走高,春节期间降至低点,开工率为6.58%,产能利用率为3.34%,之后逐渐攀升,截止6月20日,Mysteel调研全国53家独立电弧炉钢厂,平均开工率为77.73%,年同比增加13.8%;产能利用率为66.46%,同比增加6.25%。除长期停产或钢厂电炉改造等原因未开工的,其余钢厂基本复产,电弧炉开工率已经处于正常水平。
数据同时显示,截止2019年6月,Mysteel调研全国275座电弧炉,产能为1.65亿吨,计划全年新增投产2101万吨,其中已投产642万吨,未投产1459万吨。其中,华东、华南、华中地区是目前电弧炉较为集中的区域,产能占比合计73%。西南地区占样本统计的12%,未来西南地区也是电弧炉产能较为集中的区域。
2.2 废钢铁资源产生量大幅度增加
……
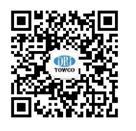
相关文章
[错误报告] [推荐] [收藏] [打印] [关闭] [返回顶部]