我国开展氢冶金的适宜工艺路线
2021-07-21
1 前言
为了应对全球变暖,2015年世界主要国家签署《巴黎协定》,我国制定了到2030年和2040年碳排放量相对1990年分别减少40%和60%的中长期碳减排目标。据国际能源署数据,2019年全球与能源相关的二氧化碳排放量约330亿吨,其中近14%是由钢铁工业产生[1-2]。2019年我国钢铁总产量9.96亿吨,占全世界总产量的53.3%,而钢铁产业CO2排放量为22.27亿吨,约占我国碳排放总量的16%,是碳排放量最多的行业之一。钢铁工业是国民经济的基础产业,对支撑其他产业发展、保障国家安全、提升国际地位具有极其重要的作用[3-4]。因此,钢铁工业有效降低碳排放强度成为碳减排计划的重中之重,低碳绿色化是钢铁工业未来发展方向。
在应对全球气候变化和能源转型的背景下,各国都高度重视无碳和低碳能源的开发利用。氢能被视为21世纪最具发展潜力的清洁能源,由于具有来源多样、清洁低碳、灵活高效、应用场景丰富等诸多优点,被多国列入国家能源战略部署。发展氢经济是21世纪世界经济新的竞争领域,中国应当审时度势,把建立取代化石能源的“氢经济”产业革命作为实现新型工业化、实现中国和平发展的重要战略目标[5-6]。将氢气用于钢铁制造的氢冶金工艺为变革性技术,是钢铁产业优化能源结构、工艺流程和产业结构,彻底实现低碳绿色化可持续发展的有效途径之一。为此,1999年徐匡迪院士提出了铁矿氢还原工艺设想,并在2002年再次提出了氢冶金的技术思想[7]。随后,国外冶金界纷纷提出氢冶金的战略规划。2018年干勇院士指出“21世纪是氢时代,氢冶金就是氢代替碳还原生成水,不但没有碳排放,而且反应速度极快”。
当前德国、日本、韩国、瑞典、奥地利等产钢国分别提出了氢冶金项目,研发热点主要有富氢还原高炉炼铁和氢气气基竖炉直接还原。富氢还原高炉炼铁项目主要有日本COURSE50、德国“以氢代煤”、韩国COOLSTAR、奥钢联H2FUTURE等;氢气竖炉直接还原项目主要有欧盟ULCOS的ULCORED新型竖炉直接还原和氢气竖炉直接还原炼钢技术、瑞典HYBRIT、德国SALCOS、MIDREX H2等,并且各自提出了不同的碳减排目标,有些甚至是碳近零排放的碳中和冶炼。当前我国钢铁生产以高炉-转炉长流程占绝对主力,绿色发展水平与生态环境需求不匹配已成为钢铁工业面临的主要矛盾。为了实现钢铁产业低碳绿色转型升级,我国高度关注氢冶金前沿技术的研发和应用,中国宝武、河钢和日照钢铁等企业分别提出了氢冶金规划。针对我国的资源和能源供应条件,合理选择适合于我国国情的氢冶金工艺路线对实现钢铁产业低碳绿色、可持续发展至关重要。
本文首先概述了国内外富氢还原高炉炼铁和氢气气基竖炉直接还原技术的研发现状,然后进行了富氢高炉和氢气气基竖炉两种冶炼工艺碳减排潜力的对比研究,得出气基竖炉是开展氢冶金的主导技术。随后,剖析了发展全氢气基竖炉工艺所涉及的若干制约问题,认为在今后一段时间内我国氢冶金应重点发展富氢气基竖炉,待相关条件成熟后再逐步发展全氢竖炉。
2 国内外氢冶金工艺研发现状
2.1 高炉富氢还原炼铁技术研发现状
2.1.1 日本COURSE50项目的高炉富氢还原炼铁
日本环境和谐型炼铁工艺技术开发项目COURSE50(CO2 Ultimate Reduction in Steelmaking process by innovative technology for cool Earth50)以“创新的炼铁工艺”为主要研究内容,通过开发高炉富氢还原炼铁技术和高炉炉顶煤气CO2捕集储存技术,将钢铁生产CO2排放减至最小,项目技术路线见图1[8-9]。研发目标是2050年日本钢铁工业吨钢CO2排放量减少30%,届时日本吨钢CO2排放将从1.64吨减到1.15吨。项目研发分为三个阶段:第一阶段(2008~2017年),其中第一步(2008~2013年)进行技术探索、优选,第二步(2013~2017年)进行以小型试验高炉为主体的“氢还原和CO2分离回收技术综合开发”;(2)第二阶段(2017~2030年),开展大型工业化试验,最终确定项目技术;(3)最后阶段(2050年左右),实现技术推广应用和普及。
高炉富氢还原炼铁是利用焦炉煤气或改质焦炉煤气替代部分焦炭,用来还原铁矿石,该向技术的目标是减少10%的碳排放,主要的支撑技术包括富氢还原铁矿石技术、焦炉煤气改质技术和高强度高反应性焦炭生产技术。焦炉煤气改质技术是通过催化裂解将焦炉煤气中的碳氢化合物转变为氢气,改质后的焦炉煤气中的氢气含量可达到60%以上。由于采用富氢煤气作为还原剂,焦比会相应降低,但焦炭还要承担料柱骨架、保障炉内煤气顺畅流动的作用,高强度高反应性焦炭的研发对氢还原炼铁技术起到了重要的支撑作用。
2013年,在瑞典LKAB试验高炉上完成了焦炉煤气喷吹的工业试验,目的是研究和评价使用普通焦炉煤气或改质焦炉煤气置换焦炭和降低还原剂比的潜力。富氢改质焦炉煤气通过炉身下部3个喷吹口喷进高炉,而普通焦炉煤气通过炉缸风口喷吹。研究表明,在炉身喷吹改质焦炉煤气能有效改善炉墙区域的透气性和增加间接还原度。得到了改质焦炉煤气的理想喷吹条件:改质焦炉煤气喷吹量应控制在200 m3/tHM以上,同时喷吹煤气的比例达到20%以上。为了支持氢还原试验,日本在新日铁住金君津厂建成试验高炉(12m3),试验高炉炉身上部安装有喷吹口。2016年4月进行了第一次试验操作,确立了氢还原效果最大化的操作技术,并对COURSE50项目第一阶段的试验技术的有效性进行了验证。结果表明,碳减排结果为9.4%,基本实现预定的碳减排目标。第二阶段将进行扩大试验,逐步模拟4000~5000 m3的实际高炉,同时进行富氢煤气加压喷吹和焦炉煤气改质整体装备研发。该项目计划于2030年在首座高炉实施富氢还原炼铁,2050年实现该技术在日本高炉的推广普及。
图1 COURSE50项目技术路线
2.1.2 德国蒂森克虏伯高炉“以氢代煤”炼铁
德国蒂森克虏伯集团与液化空气公司合作,计划到2050年投资100亿欧元,开展“以氢代煤”高炉炼铁项目[10]。“以氢代煤”目的是将H2代替煤作为还原剂,以减少钢铁生产的CO2排放。2019年11月11日,在杜伊斯堡的蒂森克虏伯钢厂,H2被喷吹入9号高炉的一个风口(见图2),进行富氢还原炼铁试验,目的是证明喷吹纯氢低碳冶炼技术的可行性和安全性。若进展顺利,计划逐步将H2使用范围扩展到该高炉的全部32个风口。此外,蒂森克虏伯还计划从2022年开始,该地区其他三座高炉都将使用H2代替煤进行冶炼,从而降低钢铁生产CO2排放,降幅可达20%。
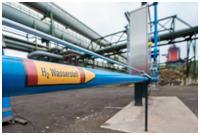
图2 蒂森克虏伯高炉喷吹氢气试验
2.1.3 韩国氢还原炼铁
韩国政府将氢还原炼铁指定为国家核心产业技术进行开发。早在2009年,韩国原子能研究院与POSCO等韩国国内13家企业及机关共同签署原子能氢气合作协议,开展核能制氢信息交流和技术研发。2010年5月,POSCO正式开发着手开发超高温反应堆(VHTR)和中小型核能反应堆(SMART)。韩国政府曾计划从2017年到2023年投入1500亿韩元(约合9.15亿元),以官民合作方式研发氢还原炼铁法:第一步:从2025年开始试验炉试运行;第二步:从2030年开始在2座高炉实际投入生产;第三步:到2040年12座高炉投入使用,从而完成氢还原炼铁。从预计投入资金情况来看,从技术研发到在2座高炉上实际投入生产,需要投入8000亿韩元(约合48.78亿元)的资金,可减少1.6%的二氧化碳排放,在12座高炉实际投入生产,预计需要投入4.8万亿韩元(约合292.68亿元)资金,可减少8.7%的二氧化碳排放。
2017年12月开始,韩国正式开始氢还原炼铁COOLSTAR项目[11]。作为一项政府课题,由韩国产业通商资源部主导,韩国政府和民间计划投入898亿韩元用于相关技术开发,其终极目标是减排CO215%,同时确保技术经济性。COOLSTAR项目主要包括“以高炉副生煤气制备氢气实现碳减排技术”和“替代型铁原料电炉炼钢技术”两项子课题。项目的第一个子课题由浦项钢铁公司主导,依据欧洲和日本的技术开发经验和今后的发展方向,以利用煤为能源的传统高炉为基础,充分利用“灰氢”,这类氢气主要通过对钢铁厂产生的副产品煤气进行改质精制而成,而非可再生能源产生的“绿氢”,由此实现氢气的大规模生产,并作为高炉和电炉的还原剂;第二个子课题是将氢气作为还原剂生产DRI,逐步替代废钢,由此减少电炉炼钢工序CO2排放,同时提高工序能效,最终目标是向韩国电炉企业全面推广。COOLSTAR项目计划2017~2020年开展实验室规模的技术研发,主要完成基础技术开发;2021~2024年开始中试规模的技术开发,完成中试技术验证,到2024年11月前完成氢还原炼铁工艺的中试开发,并对具有经济性的技术进行扩大规模的试验;2024~2030年完成商业应用的前期准备;2030年以后筛选出真正可行的技术并投入实际应用研究;2050年前后实现商用化应用。
目前,浦项钢铁公司浦项厂已将还原性副产气体作为还原剂进行应用,这类副产气体由发电站供应;现代钢铁公司利用生物质替代煤炭,由此实现炼铁工序CO2减排;浦项工科大学开发了高温固体氧化物电解电池系统,催化还原CO2,并通过间接去除技术,减少尾气中的CO2;延世大学开发的吸附工艺,从焦炉煤气中回收氢气,同时对甲烷进行浓缩;韩国科学技术院从焦炉煤气中生产氢气,并试图通过水蒸气改质工艺研究,扩大氢气的产量;釜庆大学利用炼铁副产煤气,制备高碳、高金属化率的DRI。
2.1.4 中国宝武的核能-制氢-冶金耦合技术
中国宝武的低碳冶金技术路线图[12]见图3。2019年1月15日,中国宝武与中核集团、清华大学签订《核能-制氢-冶金耦合技术战略合作框架协议》,三方将合作共同打造世界领先的核氢冶金产业联盟。以世界领先的第四代高温气冷堆核电技术为基础,开展超高温气冷堆核能制氢技术的研发,并与钢铁冶炼和煤化工工艺耦合,依托中国宝武产业发展需求,实现钢铁行业的二氧化碳超低排放和绿色制造。其中核能制氢是将核反应堆与采用先进制氢工艺的制氢厂耦合,进行大规模H2生产。经初步计算,一台60万千瓦高温气冷堆机组可满足180万吨钢对氢气、电力及部分氧气的需求,每年可减排约300万吨二氧化碳,减少能源消费约100万吨标准煤,将有效缓解我国钢铁生产的碳减排压力。
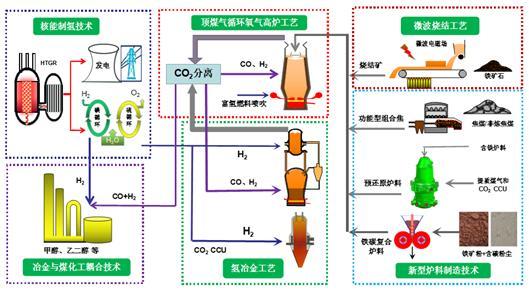
图3 中国宝武低碳冶金技术路线图
2.1.5 奥钢联H2FUTURE项目
2017年初,由奥钢联发起的H2FUTURE项目,旨在通过研发突破性的氢气替代焦炭冶炼技术,降低钢铁生产的CO₂排放,最终目标是到2050年减少80%的CO₂排放[13-15]。H2FUTURE项目的成员单位包括奥钢联、西门子、Verbund(奥地利领先的电力供应商,欧洲最大的水电商)公司、奥地利电网(APG)公司、奥地利K1-MET中心组等。该项目将建设世界最大的氢还原中试工厂。西门子作为质子交换膜电解槽的技术提供方;Verbund公司作为项目协调方,将利用可再生能源发电,同时提供电网相关服务;奥地利电网公司的主要任务是确保电力平衡供应,保障电网频率稳定;奥地利K1-MET中心组将负责研发钢铁生产过程中氢气可替代碳或碳基能源的工序,定量对比研究电解槽系统与其他方案在钢铁行业应用的技术可行性和经济性,同时研究该项目在欧洲甚至是全球钢铁行业的可复制性和大规模应用的潜力。图4给出了H2FUTURE项目的产业链。
H2FUTURE项目计划在奥地利林茨的奥钢联阿尔卑斯基地建造一个6MW聚合物电解质膜(PEM)电解槽,氢气产量为1200 Nm3/h,目标电解水产氢效率为80%以上。中试装置投入使用后,电解槽将进行为期26个月的示范运行,示范期分为5个中试化和半商业化运行,用于证明PEM电解槽能够从可再生电力中生产绿色氢,并提供电网服务。随后,将在欧盟28国对钢铁行业和其他氢密集型行业进行更大规模的复制性研究。最终,提出政策和监管建议以促进在钢铁和化肥行业的部署。2019年11月11日,计划中的奥地利林茨奥钢联钢厂6 MW电解制氢装置投产,氢能冶金时代正式开启。

图4 H2FUTURE项目的氢能产业链
2.2 氢气竖炉直接还原工艺研发现状
2.2.1 欧洲ULCOS项目的新型竖炉直接还原和氢气竖炉直接还原炼钢
ULCOS(Ultra Low CO2 steelmaking)是由15个欧洲国家及48家企业和机构联合发起的超低CO2炼钢项目,旨在实现吨钢CO2排放量降低50%或更多[16-18]。ULCOS项目主推四条工艺路线:炉顶煤气循环氧气高炉工艺TGR-BF、直接还原工艺ULCORED、熔融还原工艺HISARNA、电解铁矿石工艺ULCOWIN/ULCOLYSIS。
ULCORED工艺(见图5)主要采用气基竖炉作为还原反应器,用煤制气或天然气取代传统的还原剂焦炭,并且通过竖炉炉顶煤气循环和预热,减少了天然气消耗,降低工艺成本。此外,天然气部分氧化技术的应用使该工艺不再需要重整设备,大幅降低设备投资。以天然气ULCORED为例,含铁炉料从气基竖炉顶部装入,净化后的竖炉炉顶煤气和天然气混合喷入气基竖炉并还原含铁炉料,而直接还原铁产品从竖炉底部排出,送入电弧炉炼钢。新工艺竖炉炉顶煤气中的CO2可通过CCS技术捕集储存。与欧洲高炉碳排放的均值相比,ULCORED工艺与CCS技术结合,将使CO2排放降低70%。
在ULCORED基础上,ULCOS提出了氢气直接还原炼钢技术(hydrogen-based steelmaking),工艺流程见图6。采用H2作为还原剂,氢气来源于电解水,还原尾气产物只有水,可大幅降低CO2排放量。在该流程中,氢气竖炉直接还原的碳排放几乎为零,若考虑电力产生的碳排放,全流程CO2排放量仅有300 kg/吨钢,与传统高炉-转炉流程1850 kg/吨钢的CO2排放相比减少84%。氢气直接还原炼钢技术促进钢铁产业的可持续发展,但该工艺的未来发展很大程度上取决于氢气大规模、经济、绿色制取与储运。
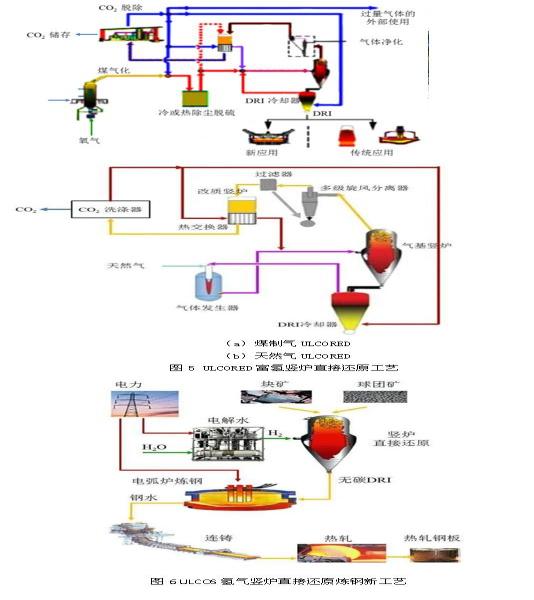
2.2.2 瑞典HYBRIT突破性氢能炼铁项目
……

相关文章
[错误报告] [推荐] [收藏] [打印] [关闭] [返回顶部]